China Leading Aerated Concrete Equipment Manufacturer
we provide a one-stop solution for your autoclaved aerated concrete block and panel making projects, from scheme design to equipment manufacturing, installation, and commissioning after-sales services.
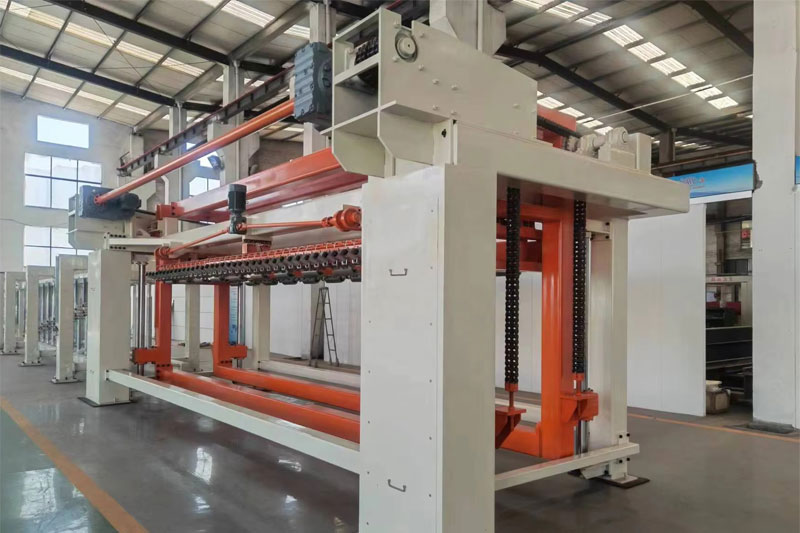
Comprehensive Solution Capability
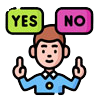
Feasibility Analysis
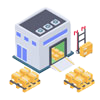
Plant Layout Design and Implementation
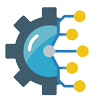
Machine Selection and Manufacturing
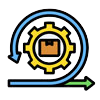
Machine Installation and Commissioning
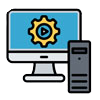
Control System Software Upgrade
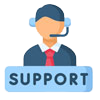
Online and On-site Technical Support
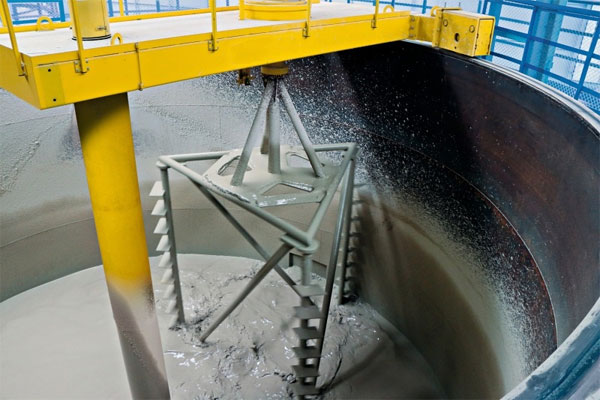
1. Raw Materials Preparation Section
Proper control and management of the raw materials preparation contribute to the production of high-quality AAC materials for construction applications.
This process involves the following equipment:
Jaw crusher
Bucket elevator
Belt conveyor
Ball mill
Dust collector
Screw conveyor
Slurry agitator
Slurry pump
2. Batching & Pouring Section
Proper batching, mixing, and pouring are essential to produce high-quality autoclaved aerated concrete blocks or panels.
This process involves the following equipment:
Powder & Slurry electric scale
Aluminium slurry mixing machine
Pouring mixer
Ferry carriage
Bubble removing device
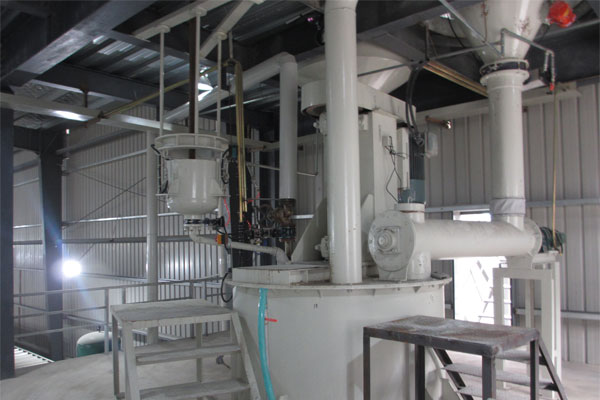
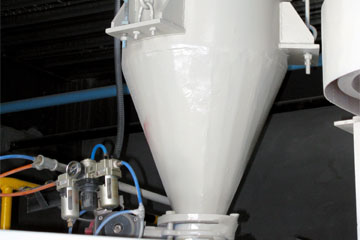
Aluminium Slurry Mixing Machine
The goal is to achieve consistent dispersion of aluminum powder and other components to ensure proper expansion and curing during autoclaving.
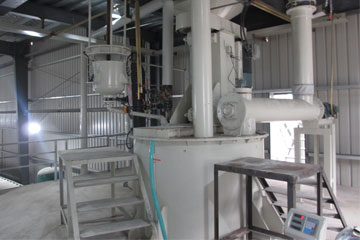
Pouring Mixer
The pouring mixer is used to evenly mix and fully react the production raw materials, and then pouring the mixed slurry into the mold frame in time.
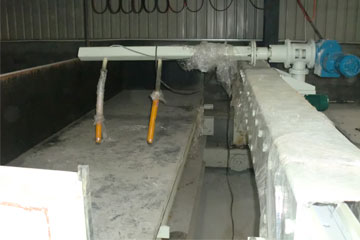
Bubble Removing Device
To ensure the structural integrity and uniform density of the AAC blocks, it's important to remove excess air bubbles from the slurry before it sets.
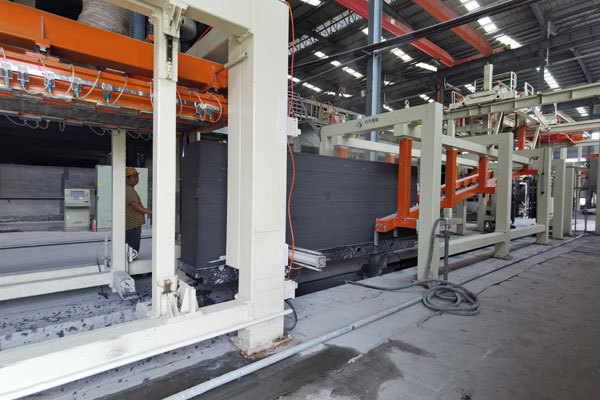
3. Precuring & Cutting Section
Both the precuring and cutting steps are crucial for producing high-quality AAC products with consistent properties and dimensions.
This process involves the following equipment:
Mould and side plate
Traction machine
Friction wheel
Oiling system
Tilting & demoulding crane
Cutting machine
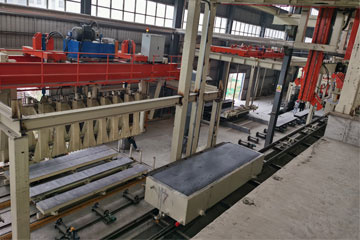
Mould and Side Plate
Side plates are used in conjunction with molds to create the desired shape and size of the AAC blocks. By adjusting plates to produce different blocks.
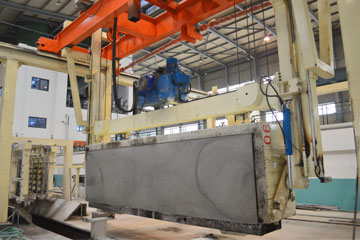
Tilting and Demoulding Crane
The tilting and demoulding crane is a specialized equipment designed to handle the delicate process of releasing the cured AAC blocks from the molds.
4. Grouping & Autoclaving Section
Once the blocks have gained sufficient strength and the chemical reactions are complete, they are grouped together for the autoclaving process.
This process involves the following equipment:
Tilting table
Grouping crane
Steaming wagon
Autoclave
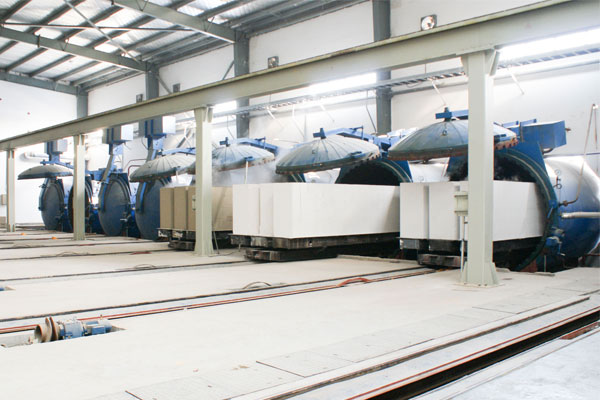
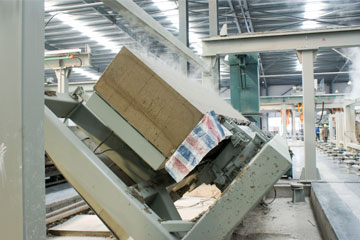
Tilting Table
The tilting table facilitates work to make the AAC block turn 90°, efficient and stable turning over, reducing the difficulty and cost of civil construction.
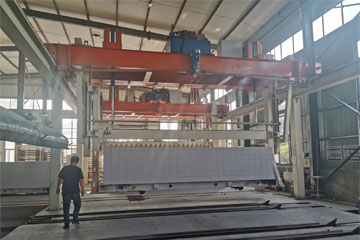
Grouping Crane
This equipment is used for smoothly and precisely grouping the newly produced AAC blocks before they are subjected to the autoclaving process.
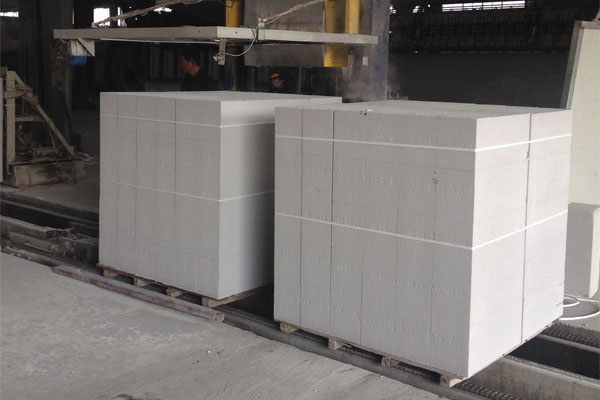
5. Packing Section
Proper packaging ensures that the aerated concrete products remain in good condition, maintaining their structural integrity and appearance until they are ready to be used in construction projects.
This process involves the following equipment:
Separator
Combination platform
Grabber
Pallet feeder
Chain conveyor
Strapping machine
Side plate clean machine
Side plate roller
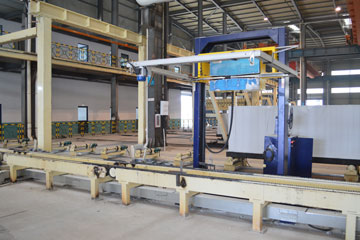
Chain Conveyor
The tilting table facilitates the initial casting, mixing, and curing of the blocks before they are ready for autoclaving, and packaging.
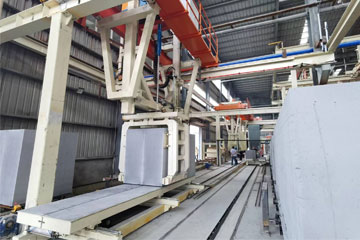
Grabber
The tilting table facilitates the initial casting, mixing, and curing of the blocks before they are ready for autoclaving, and packaging.
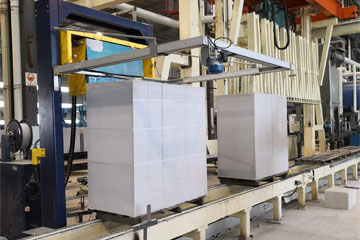
Strapping Machine
The tilting table facilitates the initial casting, mixing, and curing of the blocks before they are ready for autoclaving, and packaging.
Automation System
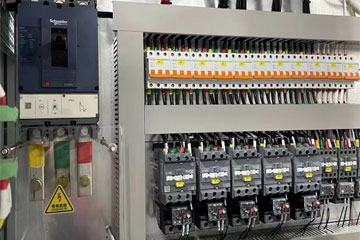
Stability
All electrical components of our equipment are imported brands, Schneider inverters, Omron/Pepperl+Fuchs switches, and Siemens programmable controllers PLC.
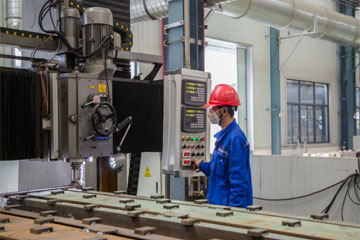
Safety
The Schneider motor protector is equipped to avoid damage to the equipment due to current overload, and also equipped with a one-button start-stop function.
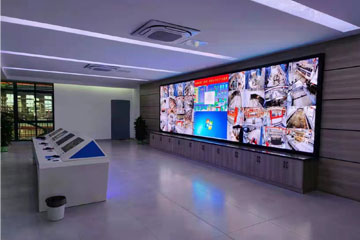
Integrate
Can set up centralized management operation stations for each production section, and can realize remote monitoring for management and troubleshooting.
Starting an AAC Block Plant?
Unleash your AAC block plant (mini, medium or large size) production potential with our industry-leading equipment. Maximize profits and minimize hassle. Your success story begins here!
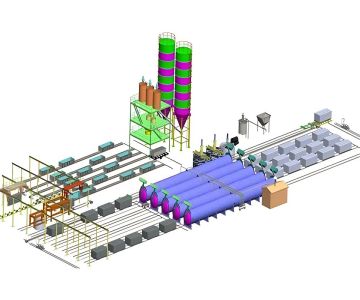
Mini AAC Plant
Capacity: 200-500CBM/Day
Factory Area: 3000 -5000M2
Main Machine: 4.2m Machines
Autoclave: 4 Sets
Cutting Machine: 1 Set
Mould and Side Plate: Mould 15pcs, side plate 162pcs
Other Machine: 1 set of ferry carriages and 3 sets of cranes
Total investment: $400,000 - $1,000,000
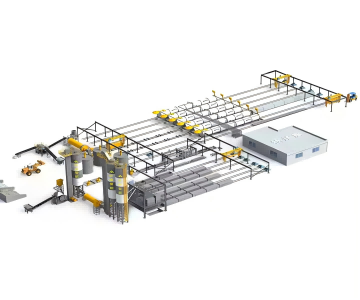
Medium AAC Plant
Capacity: 600 -1000CBM/Day
Factory Area: 5000 -10000M2
Main Machine: 4.8m Machines
Autoclave: 7 Sets
Cutting Machine: 1 Set
Mould and Side Plate: Mould 33pcs, side plate 213pcs
Other Machine: 3 sets of ferry carriages and 4 sets of cranes.
Total investment: $1,245,000 - $1,940,000
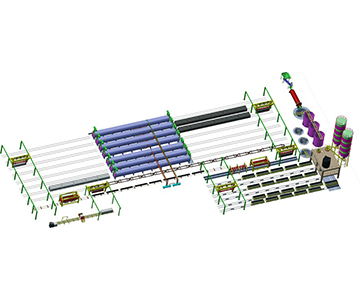
Large AAC Plant
Capacity: 1000 -1500CBM/Day
Factory Area: >10000 m2
Main Machine: 6m Machines
Autoclave: 11 Sets
Cutting Machine: 1 Set
Mould and Side Plate: Mould 53pcs, side plate 308pcs
Other Machine: 4 sets of ferry carriages and 6 sets of cranes.
Total investment: $2,180,000 - $3,470,000